 |
 |
 |
 |
 |
 |
 |
Check out our web directory of the UK
roofing and cladding industry
www.roofinfo.co.uk |
Sign up for our monthly news letter. |
|
|
In the pitched roofing industry we all know that British Standard 5250,
the Code of Practice for the Control of Condensation in Buildings, and
the Building Regulations Approved Document F2, have for many years
recommended that the way to control the build up of condensation in
roofs is through the use of ventilation. While systems that avoid the
use of ventilation have been marketed by some companies, ventilation is
still the most popular system for complying with Building Regulation F2.How it works
The basic requirements for ventilating a traditional cold loft space
are that air should enter the loft at the lowest point on one side of
the roof and exit on the opposite side of the roof. Water vapour rises
up through quilt or fibrous insulation, and meets the air in the loft,
where some of the moisture is absorbed - the quantity depends on the air
temperature.
Warm air can absorb more water vapour than cold
air. If the air layer directly above the insulation is constantly
changing it stands a good chance of absorbing most or all of the water
vapour and take it outside. The warmer the air in the rooms below the
insulation the higher the amount of moisture that can be absorbed. The
cooler the loft the less moisture that can be held before condensation
forms. Consequently if air leakage into the loft is full of moisture
then the risk of condensation forming in the loft increases. This can be
reduced if a vapour check layer is introduced below the insulation such
as foil backed plasterboard, or a layer of polythene, along with sealed
holes and openings.
Over time it is almost impossible to keep out
all water vapour from the loft. The most vulnerable period for
condensation forming in a cold loft is immediately after occupation of a
new building when the plaster walls and ceilings are drying out. Excess
water vapour finds its way into the cold loft. During cold weather the
risk of condensation forming is greater.
Extreme conditions
Air flow through the loft can discourage condensation.
Most days we have a slight breeze causing a
small positive wind pressure on one side of a roof and a small negative
pressure on the opposite side. This pressure difference can drive a flow
of air through the loft provided there are suitable air gaps on each
side of the roof linked to the loft space. But if there is no wind, then
there will be no positive or negative pressure to drive the air through
the loft.
Therefore, air that leaks through the
insulation will be warmer than the air in the loft and will try and rise
to the top of the roof. It will become trapped under the ridge and start
to cool, where it will form condensation on cold surfaces. If there was
a vent at the ridge, the air would be carried outside and cease to be a
problem.
Air should never be allowed to enter at a
ridge, only leave. It is for this reason that most roof tile
manufacturers will recommend eaves to ridge ventilation as it will cope
with both the wind and no wind situations. (Eaves to eaves ventilation
is designed to work with a slight breeze.)
There are occasions when all buildings will
experience hurricane force winds. Wind pressure will be such that the
air will pass through the loft very quickly and over-ventilate the loft.
The faster the air passes over the quilt, or fibre insulation, the less
efficient the insulation is.
Quilt insulation works by trapping air between the fibres, which forms
the insulating layer. If the air passing over the quilt can wash through
the fibres then a percentage of the air in the insulation will be washed
out and not be as efficient. It is possible to encapsulate the
insulation or cover it with a layer of material such a vapour permeable
underlay (VPU) which keeps the air in the insulation and separates it
from the colder ventilation air. Alternatively if a building is in a
very windy location it may be more appropriate to reduce the cross
sectional area of the ventilation grills to reduce the airflow through
the loft.
|
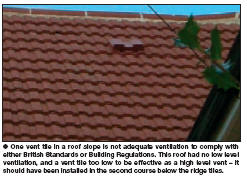 |
Recommendations
The size of the grills through which air enters and leaves a roof is
prescribed as a continuous 10mm gap at eaves or low level, with a
continuous 5mm gap at ridge or high level.
These figures are a compromise. On calm days
they are too small, on very windy days they are too large. Temperature
and moisture levels constantly change, making a precise level of
ventilation almost impossible to achieve. Although over time more water
vapour should leave the loft than enters it from below.
There is an argument that states that if you do
not have any underlay, or boarding under the tiles, and there has been
no history of condensation problems, there is no need to introduce
ventilation. The present roof ventilation requirements relate to roofs
covered with BS 747 type 1F or 5U bitumen underlay. Therefore, if a VPU
is used the amount of ventilation should be less than for a bitumen
underlay and more than for no underlay. There is no test data to
determine the correct level of ventilation. Therefore, the levels of low
and high level ventilation should remain unchanged for VPUs.
Things to avoid
There are some practices that should be avoided:
- Having ventilation tiles halfway up
the roof slope. This practice can allow condensation to form below
the level of the vents and in calm conditions still traps air up
close to the ridge
- Having a few very large vent tiles or
grills rather than a continuous slot or grill. The larger the vent
or grill, the greater the distance between the vents or grills
resulting in a massive localised air flow close to the vent and
little or no air flow as you move away from the vents
- Placing large vents on one side of the
roof directly in line with vents on the opposite side. This can
create a wind tunnel across the roof between the large vents and no
air movement as little as 600mm away
- Installing more high level ventilation
than there is low level ventilation. It is important to ensure that
air enters at low level and exits at high level and not the other
way around. If there is more ventilation at high level, air will
enter the loft at high level and drag, or suck in fog, mist or rain
The worst combination is four large vent
tiles positioned at mid span on each face of a pyramid roof in an
exposed location.
Conclusion
- Always install low level roof space
ventilation into a pitched roof
- Always try and install a continuous
grill or strip ventilator rather than large individual grills or
vents, as they provide a more even flow of air through the
loft
- Where possible install high level
ventilation to reduce condensation in calm conditions
- In very exposed locations use a VPU
over the insulation to improve the quilt insulation's performance,
or reduce the ventilation area to prevent over-ventilation of the
loft.
|
Compiled by Chris Thomas, The Tiled
Roofing Consultancy, 2 Ridlands Grove, Limpsfield Chart, Oxted, Surrey,
RH8 0ST, tel 01883 724774 |
|