Unlike tiles that have nibs to locate them on a
batten, every double lap slate needs to be twice nailed. This requires the
slates to be laid from the eaves to the ridge to ensure each nail is
covered by the slate above. Therefore to strip the slates the reverse
procedure should be adopted. But when isolated slates need to be replaced
in the middle of the roof, it may not be convenient to strip down from the
ridge in a V shape, so other procedures need to be adopted. |
Roof Access |
Once a defective slate has been identified and
marked it will need to be replaced. The first problem is gaining access to
the slate without causing more damage, and perpetuating the problem. The
use of mobile (cherry Picker) platforms to get close to the roof is second
to none. But unless the roof is steep accessing the slates will be
difficult as the slates to be replaced will be below the level of the
platform floor, or too far in front of the platform to reach. Either way
much reaching outside the platform (basket) will be needed, involving
safety harnesses and fall arrest systems. |
Working off a perimeter scaffold is an
alternative provided the distance from the scaffold to the area of the
roof needing repair, which is usually the most inaccessible part of the
roof, is reachable from a roof ladder. For a simple gable to gable roof
this will be easier than for other more complicated roof shapes. Roof
ladders make working on roof slopes safer for the roofer, but often do
more harm than good to the slate roof covering. The points on which the
ladder rests on the slates can create point loads that are liable to break
a slate. Placing cushions under the ladder helps. |
Once access to the defective slate has been achieved, the
defective slate needs to be removed with a slate ripper, which slides up
between the slates, locates above the nails and with the use of a sharp
tap from a hammer on the shaft, cuts through the copper nails. That is
provided copper nails have been used. If steel nails or screws have been
used it may be best to strip out above the slate and expose the defective
slate and fixings. |
In some instances fixings may have been driven
through the head of the slate in addition to the centre nails. In this
instance the nails may be holding the slates in the next course above, so
be careful what you cut through. If the slate has broken above the nail
holes, the top section must be removed and this may be difficult. If it
can be seen through the side lap joint, it may be possible to drill a hole
in the offending section of slate and using the drill and a slate ripper
underneath, pull the section of slate down and out. |
Matching up |
When the defective slate has been removed, and the cause of the defect
has been determined and corrected, if it is a raised nail on the course
below or it is a broken batten. The replacement of new slates should match
as closely as possible those that surround the new slate, in terms of
size, thickness, colour, texture and composition. Preferably they should
be from the same batch of slates as delivered to site. |
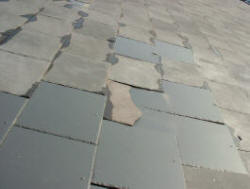 |
Replacement fixings |
The fixing of the new slates will depend upon the ability to
access the centre nail holes. If they are both visible then the slate can
be re nailed back into position using copper or other non rusting clout
headed nails. If the original cause of the problem was batten bounce or
the building is occupied with sensitive equipment or clients, screwing the
slates back may be a better option. The screws should again be non-rusting
such as Stainless Steel or Brass. Where only one nail hole is visible as
the slate is half covered by the slate above, using one patent slate
fixing, like a Jenny twin fixing and one nail or screw would be ideal.
Where no nail holes are accessible then patent secret fixing method should
be used. Under no circumstances should mastic be the primary means of
slate fixing. The insertion of a blob of mastic to restrict movement of a
loose slate may be acceptable, but not as a fixing. |
Patent Slate Fixings |
There are many patent slate fixing systems, each has a
unique feature which should be appreciated before being specified. None
are better than the original twice centre nailing of the slate into
position. There are and have been many other attempts at patent slate
repair systems, but |
Owens Jenny Twins
These are substantial aluminium units that are fixed to either side of the
slate above the nail hole position. The slate is slid into position,
whereupon a rigid wire loop swings down and locates against the head of
the batten preventing the slate from sliding out. Wind uplift resistance
is achieved by sharing the load with the slates above. |
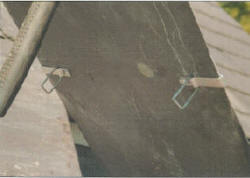 |
Red Bank Fixaslate
This is a brass plate with a central diagonal ridge with two screw holes
and a stainless steel screw. The plate is slid up the joint between the
lower slates to below the new slate. A hole is drilled through the new
slate directly above the plate and the joint in the lower slates for the
screw to clamp them together, in the same mode as a tail rivet. They are
ideal for securing loose top course slates as well as isolated slates in
the centre of a roof. The wind uplift resistance is achieved by sharing
the load with the slates below. |
 |
Ubbink Sim Fix Slate Strap
This is a plastic strap that is nailed to the batten through the slate
lap. A hook that locates under the edges of the lower slates and slides up
the strap. The strap has a ratchet that allows the hook to be slid up into
position once the slate has been positioned. The longevity of the plastic
may be an issue if the anticipated life of the roof is in excess of 20
years. However part of the wind uplift load is taken by the hook that
shares it with the slates below. |
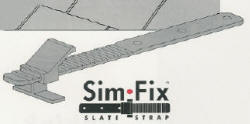 |
Nicholl & Wood Fix-A-Slate
This device is a thin stainless steel wire that locates in two holes
through the slate and allows the slate to be slid into position. Once in
position the wire drops into position against the head of the batten and
prevents the slate from sliding out. The wire is likely to outlast the
roof, however it is the most flimsy of all the products. The wind uplift
resistance load is achieved by sharing it with the slates above. |
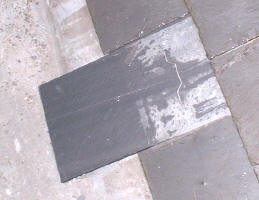 |
Conclusion |
By using the most appropriate non-rusting
fixing, when replacing a defective slate. The slate roof can be returned
to its former glory without the need to strip vast areas of the roof. This
should be quicker and cheaper without reducing the weather resistance of
the roof covering for the life of the slates |