Inverted roofs or protected membrane roofs provide one enormous benefit
compared to conventional roofs - the life expectancy of the weatherproofing
is far longer due to the effective and permanent protection for the
membrane. |
However, there is
one problem in relation to inverted roofs that until today had not been
solved: |
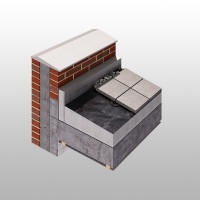 |
The Code of
Practice states an appropriate fall shall be accumulated within the flat
roof design (BS 6229) and a roof is adequately drained in accordance with BS
EN 12056-3:2000. |
A minimum fall of
1:80 is required to meet BS 6229. Creating this required fall for drainage
was a challenge… |
Jablite’s
inventor of tapered insulation for inverted roofs, Conrad Newberry, who was
a concrete technologist and is now a technical advisor in Jablite’s
innovations team, explains the issues: |
“The
majority of commercial roofs are concrete and it is very difficult to create
a fall to the rainwater outlets in concrete. Consequently the fall is
created by using a screed layer on top of the concrete,” explains Conrad. |
Unfortunately, this process of using a screed layer is beset with problems
and despite BS 6229 only around 20% of commercial roofs have the screed
layer although it is specified on about 50% of roofs. |
The problem with using screed to create fall on inverted roofs |
- After installation the screed needs to
have dried enough to receive coverings. Screed typically dries at a rate
of 1mm per day, if there is no rain during this drying out phase.
- Screeds are typically semi-dry and this
zero slump workability often results in an open surface texture which
absorbs rainfall more easily than well compacted concrete. A hair
hygrometer is the best way to determine whether a screed is dry. The
worst methods are guess work or a visual inspection!
- If the screed is not dry, any moisture
in the screed is drawn to the surface by the hot applied weatherproofing
system. This may create small bubbles in the waterproofing layer.
- Screed adds weight to a roof. Previous
RCI articles highlight screed weight has clear implications for building
frames and foundations leading to further costs. Reducing the number of
storeys in a building can impact on its commercial value.
- Screed weight can make it unsuitable for
refurbishment projects.
- The surface regularity to BS 8204 of a
semi-dry sand/cement screed is ±10mm over a 2m straight edge.
- The additional time associated with
installation and drying of the screed and the cost of suitable
structural fibres should the designer wish to expand the joints beyond
6m bays (to BS8204) all add to the total build
|
All in
all it is not surprising that many contractors and specifiers choose not to
include a screed fall. |
Many
instead opt for a zero fall roof; this is outside the scope of best
practice; however Jablite has an insulation product for a zero fall flat
roof that is BBA certified to meet this application. |
Nevertheless, at Jablite we always recommend best practice and finding a
solution to this issue exercised the mind of Conrad Newberry: “The issue of
screed falls and inverted roofs has never been far from my mind. |
“I
realised that the manufacturing processes used by Jablite for its insulation
for inverted roofs could be adapted and developed to manufacture a tapered
insulation system for an inverted roof. |
“In
addition, I knew that Jablite had the capability to design bespoke tapered
roofs as we already do that for range of insulation products designed for
the warm roof single ply market.” |
Conrad
quickly realised that his idea would solve the problems of using a screed
layer to create a 1:80 fall on an inverted roof. With a bespoke-designed
tapered insulation, an inverted roof could be specified to benefit from all
the advantages of a protected membrane installation - and still meet BS
6299. |
The benefits of Jablite tapered insulation
for inverted roofs over a screed layer are: |
- Allows contractors and specifiers to
comply with the relevant Codes of Practices and regulatory compliance
- Saves time with the removal of the
screed installation phase
- Has no drying time, Jablite insulation
boards can be laid straight onto the membrane directly over the concrete
deck
- Offers superior design to the client and
specifier
- Is a cost effective roof drainage
solution - screed costs £10/m2 more than Jablite’s tapered
insulation product for inverted roofs
- Meets BS 6299
- Weighs 2% the weight of screed
|
Accreditation and Testing |
Jablite has been awarded BBA accreditation for this latest innovation to its
inverted roof insulation range. |
During
testing of this product to the European Technical Approval Guidelines (ETAG)
031 for inverted roofs, Jablite’s innovations team discovered some
interesting aspects about the performance of its inverted roof insulation. |
“The
BBA testing found no water penetration through our inverted roof insulation
system,” says Conrad. |
“However, as laboratory testing rarely reflects real life usage, we include
an assumption of a 2.5% rainwater cooling factor in our u-value calculations
for our inverted roof insulation - to ensure they are completely reliable.” |
Additional Benefits of Jablite Insulation |
Dimensional Stability
Jablite EPS (expanded polystyrene) insulation for inverted roofs has a
dimensional stability of 0.5.
The 2% dimensional ‘instability’ of an XPS insulation board can cause
significant and unwelcome changes to the roof installation.
During a period of temperature changes such as we saw in December 2013 –
relatively warm days and below zero temperatures at night, the boards will
contract and expand.
This is the reason why XPS is rarely used in a single ply membrane system
and EPS is selected for this application |
Thermal Performance
Jablite insulation for tapered roofs can deliver any specified thermal
performance as part of a designed roof structure. |
BRE
Green Guide to Specification
Jablite tapered insulation for inverted roofs is manufactured using expanded
polystyrene (EPS) which has an A+ rating in the BRE Green Guide to
Specification. |