Over a
period of more than 20 years in the GRP roofing and architectural features
industry, there have been many advances in the manufacturing process and use
of GRP within the construction sector. |
An abbreviation
for 'glass reinforced polyester', GRP is a light, durable and astonishingly
tough constructional material which can be molded and fabricated into all
manner of products. GRP is a composite of a resilient durable resin with an
immensely strong fibrous glass. |
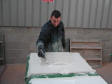 |
Polyester resin is the main component and just as concrete may be reinforced
with steel rods polyester resins may be reinforced with glass fibers to form
GRP. The benefits of a very strong and light weight construction material
are particularly relevant when designing and manufacturing structures and
roofing features. |
GRP
has opened up many new avenues for Architects and creative designers, its
unique physical properties allow it to be easily tooled, molded and
manufactured to meet almost any specification. The final finish can be made
to emulate any number of naturally occurring surfaces, such as timber, tile,
stone or lead and because there are few constraints on size, shape, colour
or finish, this can deliver great design and appearance whilst being cost
effective. |
One example of
this is the traditional clock tower. When manufactured in GRP one side is
first hand crafted in Ash timber from which a mold tool is produced. The
mold is coated with a release agent before a very durable polyester gel coat
is applied and allowed to cure before reinforcing with layers of glass mat
impregnated with polyester resin to achieve the required thickness. When
cured the laminate is extracted from the mold and the process is then
repeated. The components are then joined together to complete the body of
the clock tower. |
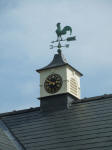 |
Ash
timber is used for the original pattern to ensure the finished product has a
beautiful realistic wood grain. Likewise one side of a roof is first dressed
in lead over a timber pattern, a mold produced and four sides manufactured
to give the finished product an authentic traditional appearance of a
genuine lead roof but without the high cost and weight of the real
materials. Another benefit of using GRP over traditional materials is that
the molds can then be cleaned and reused many times over enabling identical
units to be produced and in a very short space of time. |
GRP is also very
strong and has almost seven times the flexible strength of steel but is
extremely lightweight, which makes installation much simpler than its
traditional material counterparts, saving costs and helping to reduce Health
and Safety issues on site. GRP structures also have an exceedingly long life
span with low maintenance requirements and in a half-century of composite
development, well designed GRP structures have yet to wear out. |
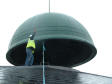 |
GRP is
non-corrosive and has a much longer life expectancy when compared to a
variety of other construction materials. In highly corrosive environments it
is the perfect choice over metal, wood, or plastic. A popular choice where
exposure to harsh environments is a concern, GRP can provide resistance to
ultra violet light, salt air, and a variety of chemicals and because it is
chemically inert and corrosion-resistant it offers an economical alternative
to stainless steel. It also offers high levels of water resistance and will
not buckle or distort in high temperatures. |
An amazing level
of detail can be given to the molding ensuring that the original style,
surface finishes, colour and even aging effects are maintained. The greatest
advantage of GRP over conventional materials however is the ability to
design and build large structures conceived as a whole and not as an
assembly of parts which have to be jointed together. For example a 5m
diameter dome requires none of the conventional support structure inside the
building, enabling a large open area within the building and space directly
beneath the dome. The self supporting structure can also be easily lifted
into position and installed using minimum man power and a crane within only
a few hours. |
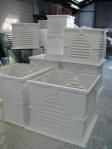 |
So not
only does GRP save time and money in the construction of the roofing
feature, it reduces installation costs and ongoing maintenance fees too,
making it an excellent cost effective roofing material for today and the
future. |
For
20 years Good Directions has been building a reputation worldwide as one of
the market leaders in the design, construction and installation of GRP
architectural features including roof turrets, cupolas and exterior clocks.
As well as a large standard range of GRP products Good Directions is always
very keen to work with clients on bespoke projects to help them achieve
their own unique designs. |
Article by Paul Mordecai, Managing Director of Good Directions Ltd.
www.good-directions.co.uk
Based in Southampton and Derby Good Directions supply across the UK and
export Worldwide. |