Over
the past 15 years or so imported slates have been the subject of both
controversy and misinformation, according to Dr Chandra Durve of Camborne
Slate, ‘the originator of the Brazilian roofing Slate and first to mine and
apply the slate on roofs’. Here he examines the issues and tries to provide
answers to a number of frequently asked questions |
In the
last two years around two thirds of claims against the NHBC Buildmark
warranty have related to pitched roofs, with those relating to slate showing
an upward trend. For roofing contractors, a better understanding of issues
affecting slate is critical if potential problems are to be identified. In
contrast to man-made roofing products manufactured under controlled
conditions by just a few predominantly European manufacturers and suppliers,
natural slate used in the UK is mined from sources throughout the world
under variable geological conditions and imported by a large number of
suppliers. Stiff price competition and tough economic conditions have
prompted the sale of low-cost material thereby prompting quality issues to
arise. |
Defining failure |
Whilst
a roofing slate is a very durable material compared to man-made products,
this durability can only be achieved by careful extraction and the
application of good quality control. Slates mined from the same area even
within metres of each other can often vary dramatically both in terms of
physical characteristics as well as quality. |
Quality relates to
the production of the complete slate from mining a geologically defined vein
rather than randomly testing finished slates. Efficient extraction involves
following veins in a rock mass with uncertain characteristics and
uniformity. The highquality roofing grade material that the UK market needs
requires proper quality control to ensure that, once applied to the roof, it
remains completely impermeable and provides a weatherproof barrier over
time. To achieve this, slates must have no interconnecting pores from one
face to the other and their fabric should contain predominantly micaceous
minerals with little or no substances which could adversely affect long-term
performance. Failure takes place if pieces of the slate begin to break away,
causing cracks or holes to appear, in contrast to aesthetic failure in which
a slate either changes colour or suffers partial delamination without
necessarily affecting waterproofing properties. Even so, the fact remains
that a change has taken place and so it is important to understand the
nature of the change in the context of failure. |
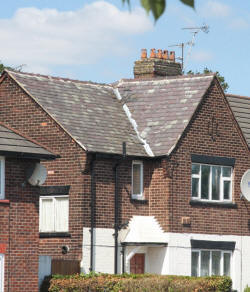 |
So,
how can failures be avoided and what quality criteria should be applied to
reduce the chances of it happening? Use of the new British Standard (BS EN
12326) is a good starting point but although it provides a good benchmark it
is not a guarantee of durability. This can only be achieved by understanding
the key factors involved in the mining of slate and examining the supply
chain or track record of the supplier. Slates which bear the genuine
Camborne mark for example, as distinct from what is said to be equivalent to
it, have been used throughout the UK by all the largest suppliers for the
past 28 years. |
The quality of slate |
Slate forms over
millions of years and like clay and concrete tiles, are formed from a mix of
fine particles. With clay tiles, rigidity results from firing a man-made mix
at high temperatures, whilst with concrete tiles a finely ground limestone
mix cures in air at normal or slightly enhanced temperature. With slate,
however, the naturally occurring mud particles carried by rivers or
deposited by volcanic activity initially settle underwater. Largest and
densest particles settle first and the smallest last with new deposits being
built up to create what are known as bedding planes. When subjected to high
levels of heat and pressure over millions of years these recrystalise to
form new mica minerals which align themselves at right angles to the applied
force. |
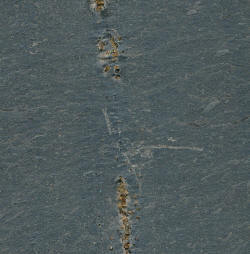 |
This
produces slate and it is this alignment which enables the slate to split
into thin sheets. Unfortunately nature is irregular and chaotic, and in
addition to carrying micas and mica-forming minerals the material also
contains small quantities of other light and heavy minerals including iron,
titanium, sulphur, calcium, manganese and even small amounts of gold! These
settle at different rates and their concentration and interaction with the
mica minerals has a major effect in determining performance. It is the
ability to identify and separate the clean masses of slate veins from the
surrounding heavily mineral-laden and unformed slate which determines
ultimate quality and performance. |
Mining variations and economics |
In a
quarry, the definition and selective mining of these veins requires
considerable skill. The grade of a slate can be controlled by continually
sampling product before and throughout the mining process and in the case of
Camborne Brazilian slates, such samples are subject to a process of analysis
driven by BS EN12326. Poor-quality material is left behind or removed to
enable continuous mining of the vein. Experienced miners can identify good
veins by colour and texture, the slate’s colour stemming from tiny amounts
of chlorite, graphite and carbon which distinguish sources such as the
finest Welsh ‘Old Seam’ Slate or the Camborne grey slate. Neither colour nor
texture, however, determine quality although such brand names are routinely
misused as generic by those seeking to sell cheaper ‘common-grade’
materials. |
Flatter slate seams as in the Camborne ZPP quarries in Brazil make open cast
mining far more economical. Nonetheless, opening a quarry requires
considerable financial investment and geological research including diamond
drilling and core sampling followed by movement of large amounts of
overburden to expose the slate beds prior to mining. The stripped material
usually contains a mix of low-grade slate and these tips often provide the
opportunity for some to produce lowcost, deceptively nice-looking slate! |
In
terms of how to avoid poor-quality slate, quality is invariably therefore
linked to price. You don’t have to be a rocket scientist to work out that
if, for example, a standard slate from Brazil costs roughly £0.30 just to
transport it, by the time importer and exporter margins and taxes have been
added there is invariably very little left to produce the slate! |
For
further information on Camborne Slate see
www.roofinfo.co.uk/camborne |
|