Metal
roofing for industrial and commercial premises, with the familiar ribbed
profile from ridge to eaves, traditionally was complemented by metal
cladding with the profile running vertically from gutter towards the ground. |
The
supporting structure for the roofing and vertical cladding is also similar
in practice, with the vertical primary steelwork crossed by horizontal
secondary steelwork. Skills acquired in roofing contracts are easily
transferred to installing vertical cladding. |
However, more and more building designs are incorporating horizontally
aligned wall profiles and panels in contrast to the vertical orientation of
the roofs. As a design statement, this has several effects, including
reduction of the apparent height and bulk of a monolithic building by
leading the eye horizontally. |
Although, this might appear to be a cladding system on its side, there are
several factors which the contractor should be aware of to ensure they are
incorporated into the contract specification and price. |
Loading the structure |
One
factor to consider is loading the structure. |
For site assembled
twin skin, using a typical "roof type" spacer grid for horizontal wall
cladding can lead to serious problems, as the spacer bracket is generally
designed to fit into the spacer bar at about 1m centres. However, because
the spacer has to stand vertically to carry horizontal sheeting, the spacer
brackets can only be fixed where the sheeting rails occur - usually at about
2m centres. Thus the spacer brackets are set too far apart and are too few
in number to carry the dead load of the cladding system. |
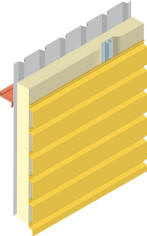 |
Typical spacer
grid brackets rely on an interference fit in the spacer bar and this
attachment is designed to resist loads acting at right angles to the grid
bar, as happens in conventional roofing, rather than the parallel load
applied when the spacer grid is standing upright. |
The
dead load of the cladding sheets have a tendency to pull the spacer bar
downwards, loading the bracket/bar joint against the interference fit which
in turn bends the bracket over. |
Spacer
system suppliers have overcome this design problem by producing more
substantial "top hat" systems with screwed together connections that can
resist the dead and imposed loads better than the lighter "roof" systems.
|
Fixing the panels |
A second factor to
consider is the placing of the fasteners. With a twin skin system, where the
gaps between portal frames may be too great for the panel length,
contractors may not be able to allow for sufficient fixings on the vertical
edges. Pull out under high wind suction, sealing and airtightness are all
potential points of difficulty. |
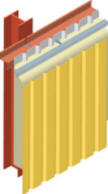 |
Where horizontal
cladding is specified for aesthetic purposes, secret fixing is frequently
desirable. Contract difficulties can arise as a result of insufficient
fasteners or poor performance from fasteners not designed for high loading.
|
A
better solution |
To minimise distortion and meet aesthetic needs,
composite (sandwich) cladding panels of insulation factory-adhered to metal
skins, are often considered the better choice for horizontal cladding
purposes.
|
With
good inherent stiffness, perpendicular or lateral panel distortion is
minimised. In addition, many composite panels are designed for secret
fixing, with overlapping tongue and groove jointing which hide fasteners.
Low profile, self-drilling fasteners within the joints and using fasteners
with thread patterns designed to protect the insulation integrity, provide
rapid, secure fixing of panels. Self-coring fasteners can also provide
additional fastening security, with a minimal external appearance. |
As
with any external envelope panel, composite panels also need the security of
25 year plus warranted austenitic stainless steel fasteners, to prevent the
risk of corrosion streaks on the once pristine façade which would ultimately
lead to claims for redress. |
Additional considerations |
If the
wall is specified as a fire wall to BS 476 part 22, any horizontal cladding
must follow the certified design detail with absolute rigour. The designs
are more complicated and costly than normal work, but the potential for fire
damage and even loss of life is so great that contractors who ignore the
detailed design will face severe consequences. |
Cladding contractors should also be aware of the special disciplines
required for installing other external wall protection such as rainscreen
cladding, which is often used in refurbishment projects. The essential
discipline when installing rainscreen cladding is to ensure absolute
flatness of the standoff support structure which carries the external skin
panels. Training by the system manufacturers and recruitment of specialist
fitters should be considered and is definitely recommended. |
With
horizontal cladding, just as with rainscreen installation, investment of
time and thought into careful prior planning will help avoid pitfalls and
ensure profitable contracts. |
For
further technical information, please contact: Peter Hamby, Product Manager
at SFS intec Ltd, 153 Kirkstall Road, Leeds. LS4 2AT Tel: 0113 2085 500,
Customer Service Fax: 0113 2085 573,or visit
www.sfsintec.biz/uk |