In Part 1, Dr Neuwald covered the various ways
in which BIPVs can be applied. In this the second part we look at the
structure of those systems, how they are implemented, the costs and return
on investment. |
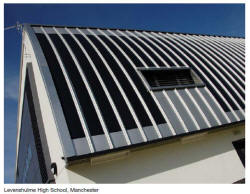 |
Structure
BIPV systems function in a similar way to the usual bolt on roof systems
which are implemented using conventional crystalline module technology. |
The PV cells which account for approximately 75%
of the system costs are connected in series to form strings of laminates
producing direct current when exposed to sunlight. |
The
strings are then routed to a combination box which gathers the whole array
together and contains a circuit breaker, fuses and – if necessary –a circuit
breaker for the lightning protection system. |
The combination box is usually installed near
the PV modules and should be easily accessible. While they are not required
in every case, their use is recommended due to the reasons mentioned above. |
The
inverter is the control centre of the PV system, accounting for
approximately 10% of the total costs of the system. Inverters not only
convert the direct current into grid compliant alternating current, they
also use voltage/amperage regulation to control the system at varying
amounts of solar irradiation. In technical jargon, this is called Maximum
Power Point (MPP) tracking. For this reason, it must be ensured that roof
extents with different orientations and pitch are connected to separate
inverters. |
The
solar energy that is generated is first used by the building and then fed
into the National Grid. In the UK, the Department of Trade and Industry’s
latest funding scheme for renewables, the Low Carbon Buildings Programme (LCBP)
was relaunched in May 2007. |
Through this, funding is available for
householders, with a maximum of £2,000 per kW of installed capacity, subject
to an overall maximum of £2,500 or 50% of the relevant eligible costs,
whichever is the lower. For the public sector there are grants available
with a maximum of £1 million or 40 to 50% of total costs excluding VAT.
|
However, in many cases the operator of a PV system is not satisfied with
merely having a feed counter.The most up to date monitoring systems permit
remote diagnostics and continuous function monitoring of the individual
components and which inform the operator of faults by, for example, text
messages or an acoustic signal. Large scale displays, which are popular with
clients, are intended to monitor the effectiveness of the system for the
operator and increase occupant awareness. |
Implementation
In the planning phase of a BIPV system, the suitability of the individual
roof and facade surfaces should first be checked in terms of irradiation
aspects. Shadowing of roof surfaces, such as can occur with prominences or
free form surfaces, should be avoided. Furthermore, minimum pitches may need
to be taken into account to ensure adequate water run off depending on the
roof system. |
Even though this
sounds complicated – especially in terms of irradiation aspects – it is
actually very simple with state of the art software. In case of doubt,
please contact our technical services department to determine the relevant
design parameters and for free annual yield calculations. |
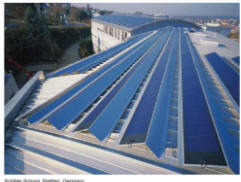 |
To do this,
suitable inverters and wiring concepts are determined so costs can be
specified and optimised at an early stage. |
Furthermore, approved planners of electrical systems and building
technicians should be involved as early as possible to reduce costs that
accrue later during implementation and prevent any duplicate planning work.
In particular, local authority policies can affect the system layout. |
It is
recommended that the local power utility company also be contacted during
the planning phase and permission obtained, along with the technical
specifications for inputting the PV system into the National Grid. |
Due to
the roof integration, the duties of roofers and electricians overlap during
implementation. However, the roofer or the facade constructor may undertake
the string interconnection of the modules and guide the additional cables
into the building. |
To do
this, they need to use special allinsulated snap-fit systems such as those
that are used in all commercially available BIPV modules. Within the
building, the qualified electrician usually does the rest of the work. He is
solely responsible for mounting the generator junction boxes, especially in
the area of the inverters and the alternating current interconnections. |
The
complete roof or facade, including the BIPV, is usually tendered as one
trade – the roof or facade constructor, with the help of subcontractors,
then undertakes the entire job up to commissioning. Modern high quality BIPV
systems can run without maintenance but this does not include scheduled
inspections of the inverters and visual checks of the PV cells for excessive
dirt or debris build up. |
Research has shown that the operation and maintenance costs of a commercial
office building over a 25-year lifetime can be up to five times the initial
capital cost of construction. The reduced running costs provided by a PV
system therefore need to be included in an economic efficiency calculation.
Maintenance contracts with the company that carries out implementation
provide certainty in this regard. These can usually be combined with
periodic maintenance work on channels, skylights and so on. |
A
frequently asked question involves cleaning work or removal of snow in
winter. In this regard, losses due to dirt are usually included in the yield
calculations but these do not include permanent deposits of rotting leaves
or of snow. |
Even
if the system were to be completely covered by snow during winter, the
annual yield would be reduced by only about 10% because the winter months
are also the period with the lowest solar irradiation. |
System
efficiency
Due to the integration of the roof system with PVs, not only are building
material costs reduced but significant savings in terms of the mounting
costs can be achieved, especially since BIPV does not require additional
assembly components such as brackets and rails. |
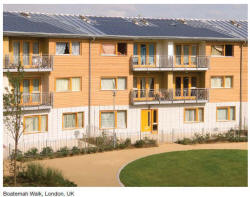 |
Due to the fact
that BIPV with thin film technology has higher specific surface area
requirements than conventional crystalline systems, the executable system
output per unit area is usually lower. |
Due to
the lower construction costs and the usually higher specific yields however,
the investment security is often higher. |
Summary
BIPV systems provide many opportunities for innovative architectural design
and they are generally less expensive than the usual add on systems. But
planning and system selection must always satisfy the structural and
physical requirements of the building shell. Selection is helped by the
multitude of fully developed and tested systems available on the market
today. |
Additional information on the planning and implementation of BIPV via an
extensive database on the basics of PVs as well as practical examples can be
found at www.AluPlusSolar.com. |
Flexible solutions for creative solar architecture are contained within an
updated Kalzip solar brochure that contains information on the different
systems available, when and how they can be installed, general design
considerations, and technical information on the advantages of amorphous
thin film technology. |
Dr
Jürgen Neuwald is director of new business and technology for Kalzip Ltd,
for more information see
www.kalzip.com |